馬啟磊1,謝紅2
(1.國電科學技術研究院,江蘇南京 210018;2.安徽省電力科學研究院,安徽合肥 230601)
摘要:對某生物質直燃發電爐排爐的爐內腐蝕情況進行分析,利用XRD對爐排渣塊、過熱器沉積焦成分進行了定量分析,利用高溫熱天平對其進行深入的熱反應動力學研究。試驗結果表明:渣塊的形成是因為物料堆積造成生物質燃料長時間缺氧燃燒熱解,成分主要是未燃盡碳。過熱器沉積焦的形成是因為生物質燃燒過程中堿金屬及堿土金屬的沉降凝結,遇高溫可再次析出。
0引言
近年來,生物質直燃發電鍋爐蓬勃發展的同時帶來了很多不同于傳統燃煤鍋爐的問題。根據國內外生物質鍋爐運行的經驗,全直燃生物質鍋爐停爐對受熱面沉積物進行清理的周期約為12個月。
木質生物質灰的硫分結渣指數約為0,堿酸比較高,硅鋁比較低。有研究指出,這些特性決定了它的灰熔點會比較高并且即使在輻射換熱面上的積灰也比較疏松。
草本生物質灰中的主要成分為Si和K,Ca和P的含量比木質生物質中的低,但是仍比煤灰的含量高。草本生物質的灰成分取決于植物種類、生長地域和土壤結構。常見生物質燃料一般收到基Cl含量超過0.5%。煙氣中K、Cl的濃度偏高會加劇爐內受熱面的高溫腐蝕。
爐內高溫下,燃料中的堿金屬類易揮發物質與煙氣、飛灰一起在受熱面上凝結、粘附或者沉降。當煙氣溫度低于飛灰軟化溫度時,沉積物大多會形成一個界限較明顯的堅硬殼,堆積以固態顆粒為主要形式。閻維平按照煤灰研究基本理論對11種生物質灰進行了分析研究,對比理論分析與實測生物質灰特性得出結論:適用于煤灰的硫分結渣指數、軟化溫度及鐵鈣比均不能正常反映生物質灰的相關特性;在草本類生物質灰的研究中發現,堿酸比、硅鋁比和硅比判別方法與界限值有一定的適用性。木質類生物質燃料,則需要研究新的判別界限;在對堿性氧化物的研究中,該指數判別生物質結渣具有相對較高的可靠性,可以在判別不同產地生物質的結渣特性或不同生物質混合燃料的結渣特性時作為重要參考依據。
1鍋爐受熱面檢查結果
鍋爐為130t/h,中溫中壓振動爐排爐,燃料以皖北地區麥秸稈為主。投產13個月后檢查發現:柔性管區域膜式水冷壁上存在大量黑色渣塊,質地疏松,輕壓可成粉末狀;爐內中溫過熱器管壁上結焦現象嚴重,部分管壁已成“炸雞腿”狀。焦塊質地堅硬致密,塊狀,呈土黃色。
2試驗結果及分析
2.1灰成分分析
由中國科技大學理化試驗中心對樣品進行X衍射成分分析(XRD)。主要分析結果如表1所示。
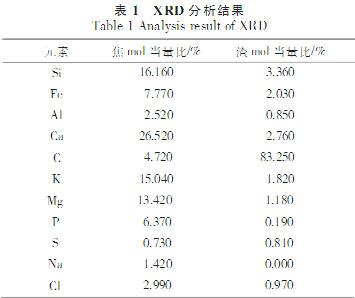
分析認為,柔性管區域渣塊的形成主要是因為落料口物料堆積造成的長時間缺氧燃燒,極度缺氧、不通風的環境下灰熔點下降明顯且局部溫度過高,造成物料缺氧熱解燒結。
2.2熱重試驗分析
2.2.1焦塊的熱重分析
將焦塊破碎并磨制成粉,利用德國耐弛公司STA409PC型熱綜合分析儀進行熱解試驗。純氮氣環境下,以25℃/min的速率升溫。焦塊熱解TG-DTG曲線如圖1所示。
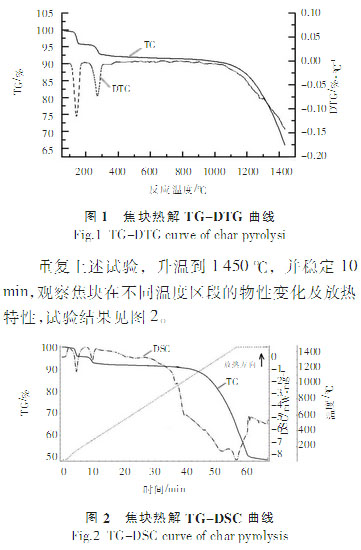
對比圖1和圖2可知,重復性試驗的TG曲線吻合性很好。
從TG曲線可以看出,樣品在30~1400℃過程中存在3次明顯的失重過程,對應有3次明顯的吸熱峰出現。第一個失重過程發生在150℃左右,為殘留水分的蒸發(電廠對爐內受熱面進行過水沖洗),伴隨有吸熱現象;第二次明顯失重發生在230~300℃,為部分低溫共晶體的揮發,伴隨吸熱現象。上述兩個過程總失重率小于10%,吸熱量均不大。在溫度為300~1000℃時,樣品質量穩定,總失重率約為2%,說明該區間樣品物性穩定。在該區間,溫度低于750℃時,樣品僅少量吸熱,此時應為吸熱升溫階段;在溫度為750~1000℃,樣品存在明顯的吸熱,但質量變化不明顯,此過程焦塊性狀改變,部分組分發生化學反應或熔融,少數揮發物析出;當溫度大于1100℃后,樣品快速失重,在1450℃維持10min后,焦塊質量不再減少。樣品總失重率達50%,在溫度為1200~1450℃時,樣品有明顯的吸熱峰出現,堿金屬共晶體或其他化合物揮發或升華,樣品物性發生改變,呈熔融狀態。
2.2.2渣塊的熱重分析
在同樣的試驗條件下,將保護氣氛改為12%氧氣,對柔性管處取得的渣塊進行了熱重分析試驗,試驗結果如圖3所示。
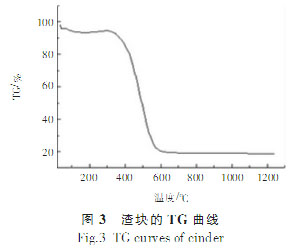
渣塊在有氧環境下加熱,失重率超過80%,燃點溫度為372℃。由此推測,該渣塊主要成分為碳。由于柔性管處為爐排進料口下方,鍋爐正常運行時大量生物質燃料堆積此處,形成深度缺氧區域。渣塊應該是生物質燃料在高溫缺氧環境下經過熱解,析出大量揮發分及部分堿金屬后所形成的焦炭沉積物。因為揮發分和可揮發堿金屬的大量析出,沉積物呈多孔疏松結構。
3調整試驗及效果
2010年3月及4月,電廠分別對1號鍋爐和2號鍋爐進行了大修,清理了爐內受熱面沉積物,大量更換了管式空預器受熱面積,其中1號鍋爐更換率為67%,2號爐更換率為63%。
同時,因為原鍋爐飛灰帶大量火星,布袋除塵系統損壞嚴重,對除塵布袋也進行了整體更換。大修結束后由電科院進行了空預器漏風率測試,測試結果表明,新更換的空預器運行效果良好(1號爐漏風率為3%,2號爐漏風率為4.2%),飛灰含碳量依然偏高,空預器入口依然帶火星。針對鍋爐情況進行了如下調整。
首先,更改爐排振動周期及持續時間。更改后振動周期為原周期的80%,持續時間增加15s。
其次,因鍋爐已經點火,無法在爐膛內部進行底部漏風整改,所以只能在爐底外側對爐排四周間隙進行。同時,大修期間電廠對爐排排渣系統進行了漏風整改,大大降低了排渣系統漏風。對空預器進口氧量測點進行校驗,并移動測點位置至代表點處;對蒸汽吹灰系統進行整體大修,保證了大修后蒸汽吹灰系統的正常投用。
最后,加強料場管理,減少入爐燃料的土灰含量。
以上整改取得了明顯的效果,送風機出力明顯增加,修正后鍋爐排煙溫度下降約12℃,飛灰帶火星情況已經徹底消失。2011年9月,鍋爐正常運行14個月后對鍋爐再次進行檢查分析發現:鍋爐最大連續蒸發量提高約15t/h;柔性管處沉積物與大修前相比變化不大。中溫再熱器受熱面高溫段已無“炸雞腿狀”沉積段存在,受熱面表面依然有一層黃褐色沉積物,但厚度已明顯降低。低溫再熱器段沉積物變化不明顯,新添加的蒸汽吹灰區域沉積量明顯少于其它區域。空預器檢查發現,高溫段已無明顯沉積及銹蝕情況出現;試驗人員用手進行觸感檢查已能明顯感覺到空預器管壁上的螺紋刻線,空預器低溫段依然存在較明顯的腐蝕現象。停爐前的空預器漏風試驗表明,兩爐空預器漏風率分別達到13%和17%。本次停爐空預器管材更換率分別為27%和30%。
4結語
在生物質直燃鍋爐受熱面腐蝕問題的研究中,沉積與腐蝕是不可分離的兩個過程。直接在金屬表面發生的氣相腐蝕極少出現,部分出現的都是表面沉積而造成的沉積物對金屬材料的堿金屬腐蝕。
煙氣中的堿金屬從生物質燃料而來,氯元素對堿金屬的析出有催化作用。在堿金屬及氯、硫元素的共同作用下,不斷腐蝕金屬壁面,而氯元素的催化搬運作用,加速氧化腐蝕。
在該爐過熱器各級受熱面的檢查發現,管壁上沉積物堆積嚴重,已嚴重影響爐內換熱效果,排煙溫度過高,但是金屬壁面無明顯腐蝕坑出現。說明過厚的沉積物隔絕了金屬壁面與高溫煙氣中腐蝕性氣體及堿金屬的直接接觸,起到了一定的保護作用,但隨著運行時間的增加,由沉積物與壁面之間發生的接觸性腐蝕不可避免。
過量空氣系數過大,造成煙氣攜帶能力增強,燃料燃燒不完全,飛灰帶火星。增加布袋除塵器負荷,影響除塵效果。
通過大修整改及燃燒調整,鍋爐經濟性及運行安全性都得到了極大的改善。但是威脅運行安全的根本因素依然存在。燃料中具有腐蝕特性的堿金屬成分的析出與沉積無法避免,從生產實用的角度而言,主要精力應集中在如何防止其在危險段沉積以及采用合適的方法對沉積物進行在線清灰,避免沉積物生長過快。以期提高鍋爐運行的經濟性、安全性,并能有效提高鍋爐蒸發量及蒸汽品質。 |