顧吉青,金保升,仲兆平,肖軍
(東南大學能源與環境學院,南京210096)
摘要:在分析國內外發展現狀的基礎上,總結了國內外相關的工藝類型和反應裝置,提出了通過生物質氣化合成甲醇、二甲醚和生物質熱解液化制油這兩條工藝途徑制取液體燃料時存在的問題,及可能的解決方案,對發展生物質轉化為液體燃料技術有指導意義。
隨著我國汽車保有量的快速增長,成品油需求日益旺盛,預計到2020年,我國的石油供需缺口為2.7億t,石油進口依存度將近60%,這對我國的能源安全形成巨大挑戰。因此開發一種可再生的、可循環使用的新能源迫在眉睫。通過將生物質轉化為高品位液體燃料,部分替代煤炭、石油和天然氣等燃料,對于增加農民收入,減少溫室氣體的排放,保障我國未來能源安全都具有極其重要的意義。生物質轉化為高品位液體燃料有兩條轉化途徑:一是生物質催化氣化合成甲醇、二甲醚;二是生物質熱解液化制生物油。
1生物質氣化合成甲醇/二甲醚
1.1技術簡介
生物質氣化合成甲醇/二甲醚流程主要包括:
原料的破碎和干燥預處理;氣化爐中氣化,生產粗合成氣;氣體凈化除去粉塵、焦油和其它污染物;合成氣化學當量比調整;甲醇或二甲醚(DME)合成及精制。為了提高整個系統的效率,降低產品的成本,經常還利用以上過程中產生的余熱、廢氣等實現熱電聯供。
1.2國外該技術研究現狀
美國能源部可再生能源研究室的PhilipsVD,KinoshitaCM,NeillDR,TakahashiPK在夏威夷中試實驗生產中,以甘蔗渣為原料,使用循環流化床反應器,在10MPa、850℃下進行甲醇合成實驗研究,甲醇產率為每噸甘蔗渣生產570kg甲醇,估計甲醇成本為每升0.22美元。
德國太陽能與氫研究中心的SpechtM,BandiA,BaumgartF,MurrayCN和GretzJ 1998年在第四屆國際溫室氣體控制技術會議上發表了題為“synthe-sis of methanol from biomass/CO2 resources”的文章,他們將生物質在循環流化床中裂解,加氫氣化催化合成甲醇,氫的添加使得生物質中包含的碳幾乎完全利用,甲醇生產速率提高,CO2去除需較少的投資強度,但由于非常低的碳轉化率(約20%),使得甲醇生產成本變得很高,一種可接受的選擇是通過添加電解氫而部分彌補碳過剩。
土爾其的DemirbasAyhan以木材鋸末為原料,在循環流化床反應器中,進行熱化學轉化制甲醇、丙酮、乙酸等化工原料的合成氣試驗,獲得了中熱值的甲醇合成氣。
由于生物質熱解氣化的原料、供應產品、需求等情況差別較大,因此,許多研究機構針對不同用途采用了相應的研究路線,并在世界各地成功運行。目前國外生物質熱解氣化選用的原料主要有①甘蔗渣,②白楊木屑,③稻草球,④松樹皮,⑤微藻類生物質,⑥稻殼,⑦木片;主要的工藝路線有①熱解氣化催化氧化,②空氣氣化催化氧化,③氧氣催化氧化,④氧氣及水蒸氣氣化催化氧化,⑤水蒸氣氣化催化氧化,⑥熱氫氣氣化催化氧化;主要的反應裝置有①固定床反應器,②流化床反應器,③加壓流化床反應器,④循環流化床反應器。
1.3國內該技術研究現狀
在生物質氣化合成液體燃料方面,我國與國際先進水平存在較大差距。國外基礎研究和技術開發已基本完成,但我國生物質氣化研究目前主要停留在氣體生產階段,深入研究較少。
中科院廣州能源研究所的常杰等,對生物質氣化制甲醇的關鍵技術和可行性進行了分析,提出了適合我國國情的技術路線;在高壓微型反應裝置上進行了生物質合成氣合成甲醇的實驗研究。東南大學的肖軍等以秸稈為研究對象,利用AspenPlus軟件建立了串行流化床稻秸氣化制取富氫氣體合成甲醇的模型,研究了不同反應條件包括氣化溫度、氣化壓力、水蒸氣與生物質(稻秸)的配比、液化溫度以及液化壓力對甲醇產率的影響。得出對于以制甲醇為目的的串行流化床稻秸氣化系統,氣化溫度建議在750℃左右,氣化壓力盡量接近常壓,S/B在0.4~0.5范圍內為佳,液化溫度建議控制在220~240℃,液化壓力選取5MPa;在此最佳工況下,每千克的秸稈可以獲得11.97mol的最大甲醇產量。
2生物質熱解液化制油
2.1技術簡介
生物質熱解指生物質在完全沒有氧或缺氧的條件下熱解,最終生成液態生物油、可燃氣體和焦炭的過程,同時也是利用熱能切斷生物質大分子鍵,使之轉變為小分子物質的過程。生物質熱解液化技術是指在450~600℃左右,103~104K/s的高加熱速率和小于2s的極短氣體停留時間下,將生物質直接熱解,且快速冷卻其產物,使中間液態產物分子在進一步斷裂生成氣體之前冷凝,從而得到高產量生物油的過程。
以流化床反應器為例,一般工藝流程包括原料的預處理、熱解以及熱解產物的分離與收集。
2.2國外生物質熱解反應器的研究現狀
反應器是生物質進行熱解的重要裝置,是目前國內外關注的焦點。表1列出了國外生物質熱解液化的主要反應器類型及主要研發機構。
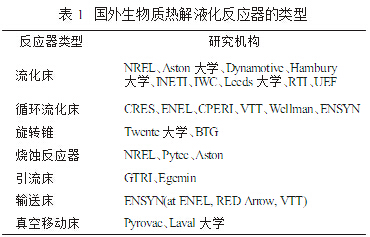
Garcia-PerezM等研究了在流化床反應器中澳洲小桉樹的熱解情況,結果表明當溫度在470~475℃時可以得到最大產率的生物油,同時進料顆粒的大小會影響生物油的含水量。VeldenMV等模擬了循環流化床反應器的快速熱解過程,結果顯示最佳的反應速率常數為0.5s-1,最佳的反應溫度為500~510℃,在此條件下生物油的產率可以達到60%~70%,這些數據與實際結果相一致。DamartzisT等模擬了在燒蝕反應器中橄欖殼在600℃溫度下的快速熱解情況,得到的結果與實驗數據具有較好的一致性。還研究在627~710℃的溫度條件下旋轉錐反應器對不同原料的生物油產率,其中,最佳的生物油產率為74%,焦炭和不凝氣的產率分別為10%和16%。VisentinV等利用引流反應器研究生物質的熱解反應,考察了不同熱解條件對生物油組成的影響,得出最佳的溫度為500~550℃,停留時間為50ms,生物質顆粒的大小為90μm。Roy研究小組的Garcia-Perez等采用軟木質樹皮(SWBR)和富含纖維的硬木質(HWRF)兩種生物質原料進行真空熱解,旨在研究不同組成的生物質經真空熱解后所得生物油的組成和性質與原料組成之間的關系。
2.3國內生物質熱解液化反應器的研究現狀
我國在生物質熱解液化方面的研究起步較晚,近年來,一批高校都開展了這方面的研究工作,并取得了一定的成績。詳見表2。
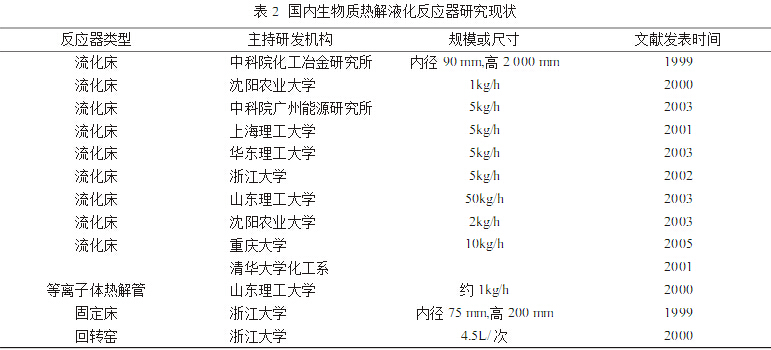
3存在的問題及建議
生物質能的利用前景十分廣闊,但真正實際應用還取決于生物質的各種轉化利用技術能否有所突破。在生物質氣化合成甲醇、二甲醚方面,國內的研究僅限于制備供暖鍋爐、發電、做飯等使用低熱值的燃氣階段,中熱值燃氣生產技術僅限于實驗室及小規模中試階段,對進一步合成甲醇技術研究還不夠,沒有生物質氣化的常壓或加壓氣化爐,采用國外的煤氣化技術,生產成本較高。在生物質熱解液化方面,國內有關生物質熱解特性、規律及反應動力學研究還相當少,缺乏描述快速熱裂解過程具有普遍意義的熱裂解動力模型,對精制產品油的分析測試還不完善,不同生物油品質相差很大,缺少統一標準。
基于上述問題,對生物質轉化為高品位液體燃料的研究提出如下建議:
⑴積極開展生物質氣化爐的研發工作,開發出擁有自主知識產權的氣化爐技術,打破國外的技術壁壘,降低生產成本。
⑵建立熱裂解動力模型,探索熱解工藝特性,優化過程控制因素,提高裝置熱解效率和生物油質量。
⑶完善生物油成分和物理特性的測定方法,制定統一的規范和標準。
⑷開發出用于熱化學催化反應過程中的低污染高效催化劑。
⑸擴大生物質燃料的應用范圍,開發適合我國使用,并具有較大經濟效益的工業化實用裝置,降低生產成本,使生物質燃料能夠參與化石燃料市場的競爭。 |